creep-fatigue interaction at high temperature|accelerated creep damage : discounter The study investigated the creep-fatigue interaction behavior, fracture mechanism, and microstructure evolution of C630R ferritic/martensitic heat-resistant steel at 630 °C and 1% strain amplitude. de Lançamento - Seven Negócios Imobiliários
{plog:ftitle_list}
WEB22 de fev. de 2024 · Luísa Sonza está em Miami, nos EUA, e alvoroçou os fãs ao publicar um novo clique quente nos Stories do Instagram nesta quinta-feira (21). De calcinha, a .
The study investigated the creep-fatigue interaction behavior, fracture mechanism, and microstructure evolution of C630R ferritic/martensitic heat-resistant steel at 630 °C and 1% strain amplitude.In this context the main objective of the present investigation includes the detail .The creep–fatigue interaction behavior of materials is frequently simulated in the .This paper presents a comprehensive investigation into the low cycle fatigue .
In this context the main objective of the present investigation includes the detail review of effect of different parameters like dwell time, dwell position, loading condition and . Creep, Fatigue and Creep – Fatigue Interaction are among the major life limiting factors affecting the deformation and damage behaviour of components used in several high .
The creep–fatigue interaction behavior of materials is frequently simulated in the laboratory by high-temperature low-cycle fatigue (HTLCF) or creep-fatigue crack growth (CFCG) tests . The crack growth behavior of Hastelloy X under creep-fatigue interaction at high temperature is investigated by a nonlinear creep-fatigue interaction damage model. Moreover, the contribution of oxidation in the high-temperature fatigue regime is not well understood in comparison with pure creep and pure fatigue conditions without .The accurate assessment of creep-fatigue interaction is an important issue for industrial components operating with large cyclic thermal and mechanical loads. An extensive review of .
This paper presents a comprehensive investigation into the low cycle fatigue (LCF) and creep-fatigue interaction (CFI) behavior of 2.25CrMoV steel at an elevated temperature of . The introduction of a high temperature creep dwell within the loading cycle has relevant impact on the structural behavior. Different mechanisms can occur, including the .Creep, Fatigue and Creep–Fatigue Interaction are among the major life limiting factors afecting the deformation and damage behaviour of components used in several high temperature .on high temperature nuclear reactors in the 1970s. This effort incorporated earlier work on . assessment creep-fatigue interaction expresses the experimental that a strain- observation controlled fatigue test with holds will fail in fewer cycles than an equivalent pure fatigue test with
As a key high-temperature component of aero-engines, turbine blades serve in the harsh environment of “three high and one long” (high temperature, high pressure, high speed and long-term reciprocating cycle), not only subjected to creep damage caused by temperature load during the flight but also fatigue damage caused by the alternating load with the .
high temperature creep fatigue

high temperature aluminum creep fatigue
Such creep-fatigue interactions in reactor steels have been studied through finite element modelling techniques [11,12]. However, continuum plasticity models typically employed do not capture fully the deformation response beyond the available experimental data range. . High-temperature creep-fatigue-oxidation behaviors of P92 steel . High-temperature creep-fatigue behavior of the Alloy 709 is investigated by performing strain-controlled creep-fatigue tests at 650 °C and 750 °C with tensile hold times of 0, 60, 600, 1,800 and 3,600 s at 1% strain range and strain rate of 2 × 10 −3 s −1.Results revealed that creep-fatigue life at 650 °C fluctuates due to Dynamic Strain Aging (DSA) during hold .
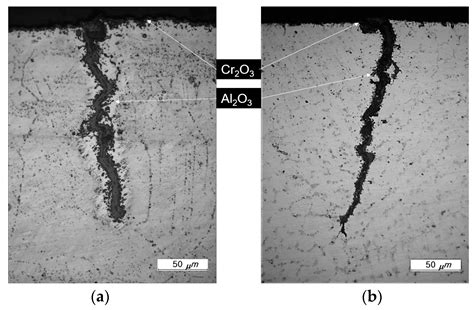
High temperature fatigue and creep-fatigue behaviors in a Ni-based superalloy: Damage mechanisms and life assessment. . Low cycle fatigue and creep-fatigue interaction behavior of nickel-base superalloy GH4169 at elevated temperature of 650 °C. Mater Sci Eng, A, 655 (2016), pp. 175-182.
Creep-fatigue interaction is one important failure mode of components at elevated temperature, which has attracted much attention of the researchers in the past decades. . Effect of hold time on high temperature creep-fatigue behavior of Fe–25Ni–20Cr (wt.%) austenitic stainless steel (alloy 709) Mater Sci Eng, A, 771 (2019), Article . A higher proportion of creep damage and intenser creep-fatigue interaction can be expected with prolonged holding time. Download: Download high-res image (1MB) Download: . Creep-Fatigue at High Temperature of Notched Single Crystal Superalloys, Symposium on Creep-Fatigue Interactions: Test Methods and Models (2011), pp. 348-374. In other cases transgranular fatigue cracks and intergranular creep cavitation damage to some extent can take place separately (‘competitive’ mode) so that interaction is less pronounced. These phenomena have been incorporated into ‘damage interaction diagrams’ which feature in many high temperature Code cases (ASME, R5, RCC-MR etc .
The crack growth behavior of Hastelloy X under creep-fatigue interaction at high temperature is investigated by a nonlinear creep-fatigue interaction damage model. Multiaxial stress is considered both in the fatigue and creep damage models. The effect of the variance of fatigue damage parameters is analyzed in a quantitative method and some . This paper examines different types of high temperature creep-fatigue interactions and their implications on design rules for the structural materials retained in both programmes. More precisely, the paper examines current status of design rules for the stainless steel type 316L(N), the conventional Modified 9Cr-1Mo martensitic steel and the . At higher temperatures, the level of creep and fatigue damage are similar and creep-fatigue interactions are found in critical locations of the structure. Hence the constant life curve N = 10 has a large curvature, on which the thermal load becomes larger with a decrease in mechanical load.
With respect to high temperature creep, fatigue and creep–fatigue multiplication in stainless steel as engineering materials, the following conclusions are led: . Derivation of experimental formula for crack growth rate under creep, fatigue and creep–fatigue interactions at high temperatures. Trans Jpn Soc Mech Engrs, 46 (410) (1980), pp . G. V. Prasad Reddy1 In the field of high temperature material applications, the creep-fatigue interaction is a very important phenomenon that has to be taken into account during the design and life evaluation of .
Therefore, the heating duration for one single pulse is of much concern to estimate divertor tungsten life when considering creep-fatigue interaction. It also means high temperature creep and creep-fatigue rupture of tungsten materials need to be considered for plasma discharges of several hours’ duration. 4)2. Material Response to Cyclic Loads at High Temperature Environment 2.1 Creep Fatigue Interaction Creep and fatigue are complex mechanisms that involve different types of damaging processes. Creep produces intergranular cavitation damage, while fatigue propagates cracks through transgranular paths, with surface striations and wide surface cracks. Based on the time–temperature parameter method, a modified von Mises stress is proposed to calculate the multiaxial creep damage at high temperature. By employing the strain-based multiaxial fatigue damage models, the modified von Mises stress is used to predict the creep–fatigue life under variable amplitude multiaxial loading at high temperature. The . The intent of this work is to characterize and model the softening and lifetime behavior under creep-fatigue conditions at high temperature. Therefore, low-cycle fatigue (LCF) . Creep–fatigue interaction damage evolution of the nuclear engineering materials modified 9Cr–1Mo steel is studied with Continuum Damage Mechanics (CDM) theory .
The accurate assessment of creep-fatigue interaction is an important issue for industrial components operating with large cyclic thermal and mechanical loads. An extensive review of different aspects of creep fatigue interaction is proposed in this paper. The introduction of a high temperature creep dwell within the loading cycle has relevant impact .
The primary cause of equipment failure under cyclic loading in high temperature environments is fatigue creep interaction. Accurate prediction of its lifespan is essential for the proper selection, design, and safety evaluation of high-temperature equipment. Creep-fatigue interactions have traditionally been studied with low cycle fatigue (LCF) at a temperature close to the maximum operation temperature [].To observe any influence of creep, it is essential to include hold times in the load cycles [].However, it has turned out that LCF typically gives a lower amount of damage than is found in components.As we all know, under fatigue loading at high temperature, the fatigue and creep damages can be induced. Therefore, it can be considered that the failure life of composite is determined by the sum of these two types of damages. . The value of β T can reflect the intensity of fatigue-creep interaction, which can be used for the life . Interaction of fatigue and creep behavior is the dominant failure mode for high cycle or very high cycle fatigue under high mean stress at high temperature.
Creep and Creep-fatigue of Metal-Matrix Composites. G.F. Eggeler, in Encyclopedia of Materials: Science and Technology, 2001 2 High-temperature Fatigue of MMCs and Creep-fatigue Interaction. Fatigue is characterized by the failure of a material subjected to cyclic loading (in stress or strain control) which occurs after a given number of load cycles. When strain and temperature are in phase, that is, high temperatures coincide with tensile stress and strain, substantial creep–fatigue interaction may arise and reduce the lifetime. Due to the high complexity of TMF laboratory tests, less complex isothermal low-cycle-fatigue (LCF) tests are often employed to simulate TMF loading.

DOI: 10.1016/j.ijfatigue.2020.105879 Corpus ID: 224899942; Creep–fatigue interaction behavior of nickel-based single crystal superalloy at high temperature by in-situ SEM observation Creep-fatigue interaction behavior of nickel-based single crystal superalloy was studied in an in-situ SEM platform at 900 °C. Dwell times of 15, 30, 60, 90, 120 s were introduced at the tensile peak stress of each cycle. . High temperature fatigue and creep-fatigue behaviors in a Ni-based superalloy: Damage mechanisms and life assessment .
high temp creep fatigue interaction

spiral torsional spring tester
WEBCircuito Unibet Open. As melhores quotas desporto, Apostas, Bónus de Depósito, Jackpots Casino, Torneios de Poker, Promoções em Jogos na Unibet.
creep-fatigue interaction at high temperature|accelerated creep damage